EVIC home page
EVIC
Update #19 - March 31, 2004
The McQueen
EVIC
David McQueen started this engine in the spring of 2003. Unfortunately, David lost interest in the project and as a result sold the uncompleted engine to me in January 2004. I completed the engine and ran it for the first time on March 8th. Compression was poor and the engine would not run below 3500 rpm. A new piston was constructed and installed on March 11, 2004. With the new piston performance met all expectations. The "Electronic Throttle" and the Hit and Miss demo work well. See photo on home page. There are additional photos on this web site and there are about 20 construction photos of this engine on the Yahoo Groups EVIC web site. http://groups.yahoo.com/group/EVIC-111/
This EVIC - 111 has the Mk2 head design but is only using one Bicron solenoid per valve. It is running with the Mk2B electronics and will be used for demonstrations at model engineering shows. The current "ET" speed range is 1300 to 7000 rpm. It has a built up aluminum crankcase. The crankcase volume has been increased as recommended in Rev. 4 of my book by making the crankcase the full width of the base.
This engine has modest valve lifts. The intake lift is 0.032" and the valve spring provides 2lb 2oz of force. The exhaust lift is 0.028" and the valve spring provides 2lb 0oz of force. The engine is running with the September 2002 Mk2B software. The simple carburetor has a venturi of 7/32" that gives good fuel draw over the entire speed range.
The Bristol University
EVIC Project
Last week I received the following E-mial message from a group of mechanical engineering students in Bristol England:
Sent: Monday, March 22, 2004 5:36 PM
Subject: Re: Engine Project
Dear Dave,
Despite all the pessimistic attitude within the department with regard to the engine, in that it would never run, in the early afternoon of Thursday of last week, four Bristol students got a Honda C50 engine running on solenoids. Check out the web site below with some photos of the rig and a video clip of it running. We managed to get it up to 1800 rpm but our 2mm lift on the valves limited us to this. We ran out of time to experiment with higher lift but it gave us great pleasure to get it going at all. Big grin on our tutors faces. I'd like to take this opportunity to thank you for all your help throughout. It has been so fundamental to our success and we are thinking of calling it the DB1 (Dave Bowes 1). I'll send you a photo of us and a copy of the final report if you wish.
Thanks again.
Mark www.britishspirit.co.uk …. It's the i-valve engine section.
Below is a sketch of the solenoid arrangement and a photo of the happy students; Andy, William, Rob and Mark.
---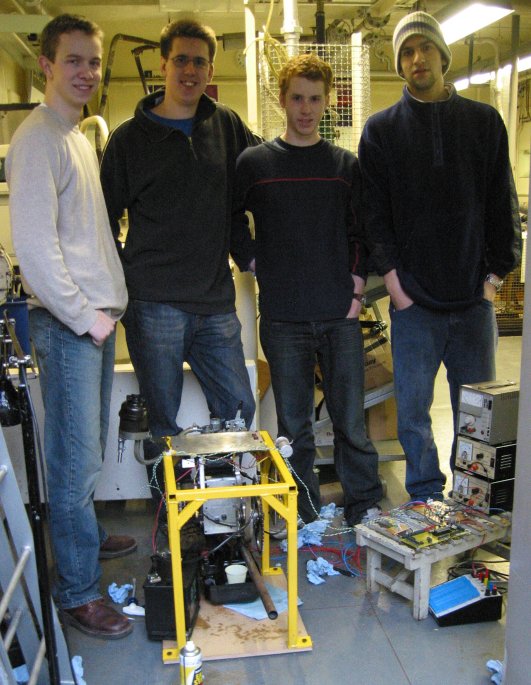
Other Student Projects
I have also enjoyed offering assistance to students doing solenoid operated valve engine projects at universities in Canada, USA, West Indies and India. There is an engine at UCLA almost ready to run. I offer assistance to all students who ask.
Experiments with my 2nd EVIC -111 Single
Eddy Current reduction in Solenoids
At the Cabin Fever Expo model engineering show I met two fellows, Gary Bergstrom and Joe Seale, who have considerable expertise in solenoid design and their application to I.C. engines. Based on their advice I was able to reduce the eddy currents in my solenoids. For details see the Yahoo Group EVIC web site http://groups.yahoo.com/group/EVIC-111/ or send me a E-mail request. With reduced eddy currents the solenoids run cooler and respond more quickly when the coil current is removed. I was hoping that this would lead to a higher top speed but to date this has not happened. I believe stronger springs and an increase in the holding voltage/current are required to boost the top speed into the 13,000 to 14,000 rpm range. With the existing valve configuration the valves appear to start to float at ~11,600 rpm.
2nd Intake Valve Solenoid
Last time I reported adding a second intake valve solenoid and that this addition hadn't led to improved high speed performance. This hasn't changed. However I have used the dual solenoid configuration to implemented two intake valve lift steps. The lower 0.020" lift is used when the engine is throttled and results in an improved idle. Full 0.055" lift is used when the throttle is opened more than 1/2. As most of you know I am throttling the engine solely by changing valve timing so there is no throttle restriction in the intake manifold. When an engine is throttled by changes to valve timing the idle speed tends to be somewhat unstable. The reduced intake valve lift helps to improve stability. I have also added a simple software idle speed regulator to further improve idle speed stability. This regulator is included in the March 2004 revision 2 of the Mk4 software.
The EVIC Twin
I haven't made any changes to the Twin since October. I hope to have drawings for the Twin available at NAMES.
Electronic Fuel Metering - EFM
I have done a number of tests on the electronic fuel metering system. It works but I haven't come up with a fully satisfactory calibration yet. I plan more work after NAMES.
NAMES 2004
I will be at NAMES this year with 4 EVIC engines. At noon on Saturday I am giving a seminar on Improving the Reliability and Performance of Minature I.C. Engines. This is not an EVIC engine seminar. The focuses is on tips and techniques for improving all I.C. engines. Come and bring a friend. NAMES is April 24-25 at the Southgate, MI, Civic Center. www.modelengineeringsoc.com
The EVIC Group on Yahoo
http://groups.yahoo.com/group/EVIC-111/
Dave Bowes, EVIC Designer
EVIC home page